Posts Tagged ‘homebrew’
On Making Nanowaves – Part 4
Researching suitable LEDs for our lightwave project forced me, once again, to the bottom of the learning curve. Like the variety of photodiodes being used in simple lightwave systems, there were a myriad of LEDs experimentally lighting up the skies both in the UK and in the U.S.
It seemed that the present flavor-of-the-day in terms of LEDs was the Luxeon III, a 3W / 1.4A device being produced by Phillips.....or rather.....was being produced. Apparently our new found interest in lightwave communications had been coincidental with the retirement of this popular LED and all stock had been depleted! Although still available in some wavelengths, there were none in the desired 'deep red' portion of the spectrum that we had chosen for our system.
All was not lost however as a 'replacement', largely untested by the lightwave community, spec'd-out at a lower power but with a somewhat more efficient design. The new device was the Luxeon 'Red Rebel' and rated at 700ma. ....apparently no slouch at all.
I had also been watching the various offerings available on e-bay which provided a number of tantalizingly inexpensive options. Many of the LEDs from China appeared to offer good promise and may well be good performers, but most appeared to be lower-quality knock-offs of the name-brand models.
These higher-powered LEDs, on close examination, usually contained two or more separate LED die behind the lens. A single light source is required to achieve maximum focusing / lens illumination efficiency and although tempting, should probably be avoided. 'Safe' names to look for include Philips, Osram and Luminus and often, bargains can be found on e-bay when NOS is being disposed of.
Like most 'power' LEDs, the Rebel needs to be mounted on a heatsink otherwise catastrophic destruction would be immediate. The usual method of heatsinking is to attach the LED (by solder or adhesive) to a copper star-shaped interface which is then fastened to a small heatsink.
The interfaces can be purchased separately but soldering the LED can be challenging without overheating it. They can also be fastened with JB Weld and enough pressure to ensure a firm bond without damaging the LED. An easier alternative is to procure the LED already mounted on the interface as shown here.
Once adequately heat-sunk, voltage can be applied to the LED after taking measures to limit the current to safe levels. Although these LEDs are very small, they emit an exceptionally bright light and must be treated with care. The Rebel is shown here, shortly after first applying voltage. The current in this test was just 100ma. Although they are rated at 700ma, I have run this one up to 1A without failure but it is normally run at the rated current.
The next task was to tackle the 'antenna' which, in a lightwave system, is the lens. Many of the UK amateurs were having good results with inexpensive 4"-5" magnifiers mounted inside ABS or PVC tubing. The remainder, and those in the U.S., were using plastic Fresnel lenses mounted in homebuilt plywood boxes of various designs. Clint's (KA7OEI) website contains a vast amount of valuable hands-on info describing the latter and we chose to go via that route.
Like the large variety of both photodiode and LED selections, fresnels were no different. Once again there was a lot of information to digest while learning about the various types. Eventually, John, Markus and myself each purchased two plastic fresnel lenses from 3DLens in Taiwan. One would be used in the receiver box while the other was for the transmitter. These were 26cm square lenses, model A260.
Unfortunately I no longer see these particular lenses being offered....hopefully it is only a momentary depletion of stock. There are many different sizes and types of fresnels out there....some if them perfect for this type of use and others not so good, so think carefully before buying anything and know what you are getting. Studying Clint's pages regarding fresnels will help immensely.
Things to pay attention to are the focal length and groove 'pitch'. For a typical 10"-12" lens, look for something around 10-12" focal length, otherwise the mounting enclosure will get too deep and awkward to handle. Front surface 'groove pitch' should not be too fine...something around .5mm is good but our finer (.2mm) seemed to work well also.
Now that the LED had been mounted and the fresnel lenses were in hand, the next task would involve the focusing mechanism and alignment. Thankfully John had devised a smart method for mounting and adjusting focus a few weeks earlier, when we were still working on receivers.....
It seemed that the present flavor-of-the-day in terms of LEDs was the Luxeon III, a 3W / 1.4A device being produced by Phillips.....or rather.....was being produced. Apparently our new found interest in lightwave communications had been coincidental with the retirement of this popular LED and all stock had been depleted! Although still available in some wavelengths, there were none in the desired 'deep red' portion of the spectrum that we had chosen for our system.
![]() |
Courtesy: http://www.luxeonstar.com/luxeon-rebel-leds |
All was not lost however as a 'replacement', largely untested by the lightwave community, spec'd-out at a lower power but with a somewhat more efficient design. The new device was the Luxeon 'Red Rebel' and rated at 700ma. ....apparently no slouch at all.
I had also been watching the various offerings available on e-bay which provided a number of tantalizingly inexpensive options. Many of the LEDs from China appeared to offer good promise and may well be good performers, but most appeared to be lower-quality knock-offs of the name-brand models.
These higher-powered LEDs, on close examination, usually contained two or more separate LED die behind the lens. A single light source is required to achieve maximum focusing / lens illumination efficiency and although tempting, should probably be avoided. 'Safe' names to look for include Philips, Osram and Luminus and often, bargains can be found on e-bay when NOS is being disposed of.
Like most 'power' LEDs, the Rebel needs to be mounted on a heatsink otherwise catastrophic destruction would be immediate. The usual method of heatsinking is to attach the LED (by solder or adhesive) to a copper star-shaped interface which is then fastened to a small heatsink.
![]() |
Courtesy: http://www.luxeonstar.com |
Once adequately heat-sunk, voltage can be applied to the LED after taking measures to limit the current to safe levels. Although these LEDs are very small, they emit an exceptionally bright light and must be treated with care. The Rebel is shown here, shortly after first applying voltage. The current in this test was just 100ma. Although they are rated at 700ma, I have run this one up to 1A without failure but it is normally run at the rated current.
![]() |
Luxeon Red Rebel at 100ma. |
Like the large variety of both photodiode and LED selections, fresnels were no different. Once again there was a lot of information to digest while learning about the various types. Eventually, John, Markus and myself each purchased two plastic fresnel lenses from 3DLens in Taiwan. One would be used in the receiver box while the other was for the transmitter. These were 26cm square lenses, model A260.
Unfortunately I no longer see these particular lenses being offered....hopefully it is only a momentary depletion of stock. There are many different sizes and types of fresnels out there....some if them perfect for this type of use and others not so good, so think carefully before buying anything and know what you are getting. Studying Clint's pages regarding fresnels will help immensely.
Things to pay attention to are the focal length and groove 'pitch'. For a typical 10"-12" lens, look for something around 10-12" focal length, otherwise the mounting enclosure will get too deep and awkward to handle. Front surface 'groove pitch' should not be too fine...something around .5mm is good but our finer (.2mm) seemed to work well also.
Now that the LED had been mounted and the fresnel lenses were in hand, the next task would involve the focusing mechanism and alignment. Thankfully John had devised a smart method for mounting and adjusting focus a few weeks earlier, when we were still working on receivers.....
e-Bay PCB Thermal Transfer Paper
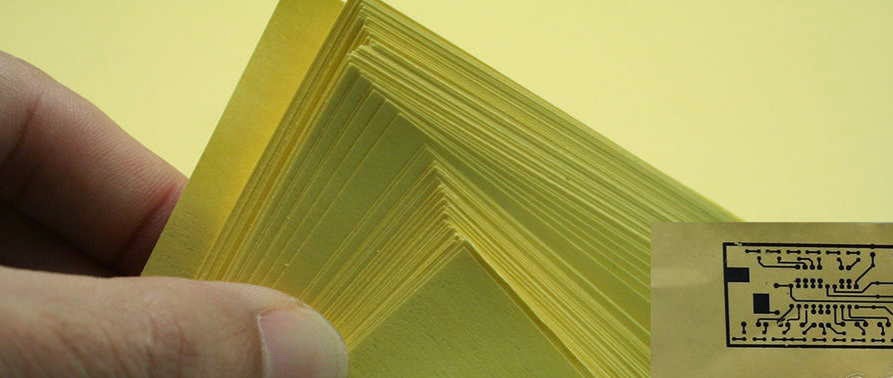
My new paper from China (free shipping!) was pretty inexpensive and if it offered even a slight improvement, would be well worthwhile. This first use of the paper would be a circuit board for my earlier test-bed GW3UEP 630m transmitter. I had finished designing a PC pattern for it, using MS Paint, and was anxious to see the results.
![]() |
Courtesy: http://www.gw3uep.ukfsn.org/ |
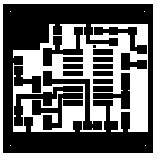
I know that a lot of folks turn up their noses at MS Paint but I have always found it to be a very versatile piece of software and have used it for making PC layouts for many years. I also use it for drawing all of the schematics appearing on my website.
After printing the pattern (printer set for maximum resolution and darkest print) and ironing-on the pattern , I allowed the board to cool for several minutes before immersing it, along with the now firmly attached yellow paper, into cold water. The first thing I noticed was how easily the paper came away from the board. It actually 'un-peeled', much like a good quality price tag sticker...you know.... the ones that don't take forever and come off in tiny bits and pieces. It peeled off smoothly with no paper residue left on the board. This was a huge improvement already. There were just a few traces of toner left on the paper as almost all had been transferred to the board.
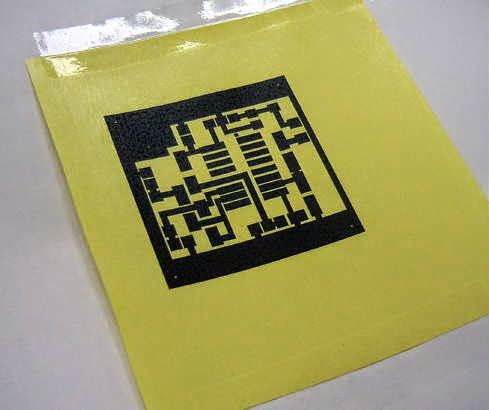
Another recent change in my PC etching regime has been a switch from the old Ferric Chloride standby to a combination of Hydrogen Peroxide and Muriatic acid. Not only does it seem to etch more cleanly (no undercutting) but it also etches very quickly and without any solution warming needed. This board was completely etched in just over 4 minutes.
The chemicals used in this method are inexpensive and are readily available at the drugstore and at the hardware store. There are numerous web-descriptions of this particular etching process but this site seems to cover the basics nicely.
The completed board turned out as shown here:
The CD4060 not only functions as a crystal oscillator but also as a versatile frequency divider. As well as fundamental frequency output, ten different 'divide-by' functions are available depending in which output pin is chosen. These range from divide-by 16,384 to divide-by 16. This circuit uses the latter, dividing the 7.6 MHz crystal down to 475 kHz at pin 7.
In summary, I can highly recommend the e-Bay yellow thermal transfer paper when used for this method of making PCB's and is much cheaper than buying photo-quality printing paper.
On Making Nanowaves – Part 3
Having studied many of the receiving systems being used by others, it seemed that designs ran from the 'very simple' to the 'very sophisticated'. Once again I looked to Roger's experimental work involving receivers since the one he had been using had evolved over a period of several months and several tweaks. The design that he used was an adaptation of the original low-noise PIN diode laser receiver designed several years ago by K3PGP and shown here on K3PGP's Experimenter's Corner.
Roger's adaptation, shown below, appeared to be getting excellent results when used in his over-the-horizon clear air scattering tests.
Although Markus, John and myself all built the same design, it is interesting to see the end results, as each used a different construction method.
John chose to use perfboard and point to point-to-point wiring:
![]() |
VE7BDQ's Perfboard RX |
![]() |
VE7SL's PCB RX |
![]() |
VE7CA's Dead-Bug Style RX |
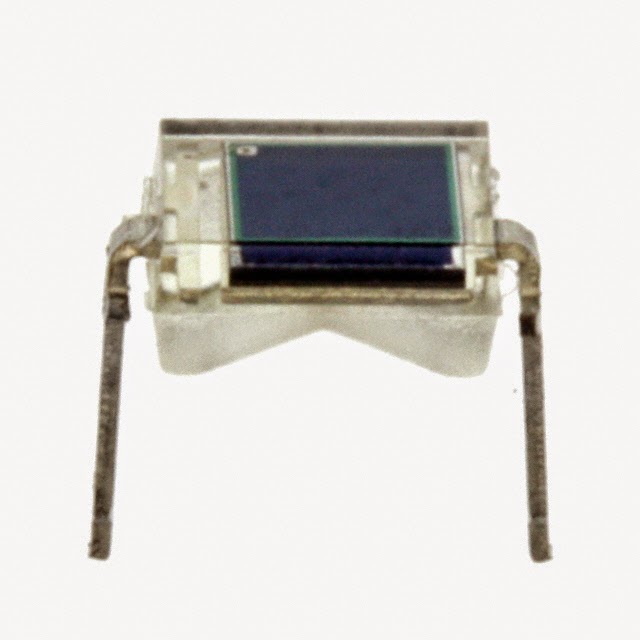
![]() |
BPW34 Spectral Range |
Many silicon PIN photodiode detectors are available with filters that let them achieve maximum sensitivity at the lower IR range while blocking the unwanted higher frequency visible light sources. Such is the case with this one, available as the BPW34FA. If you wanted to run an all IR system, reducing visible light QRM, this detector might be a better bet.
![]() |
BPW34FA Spectral Range |
When it comes to diode detectors, there are always new challengers appearing in the marketplace. There are still many opportunities for experimenting when it comes to optimizing the front-end of your receiver.
When coupled with its focusing lens in the final stage of construction, the receivers are amazingly sensitive. Even the slightest hint of a light source, often invisible by eye, would produce a response from the system....even starlight!
One of the first sounds detected was a low-pitched and repetitive 'thump-thump' which turned out to be the wingtip strobe lighting of jet aircraft activity approaching and departing Vancouver International Airport. After several nights of listening it was apparent that the strobe lighting could be detected from at least 70 miles out and from aircraft still above 10,000'. Panning over to the runway (about 25 miles away), I could often detect the strobes from departing aircraft even though they had not appeared above my sea-level horizon. Eventually I would see them rise above the horizon, about a minute after hearing them on the runway while on their takeoff roll. I suspect the propagation mode would be a form of clear-air scatter since there was no direct line-of-sight to the signal source when initially heard.
Panning the receiver slowly along the many miles of coastal mainland, on the other side of Georgia Strait, revealed many signals, most of them with different audio signatures. Some sounded rough and buzzy, like an unfiltered CW note, while others were T9 and very clean. Most had different repetition rates resembling radar sweep speeds but, once again, most sources were not visible to my eye...nor were they located when scanning the signal source with binoculars. I suspect that most signals were from various fixed lighting installations either strobe lighting or area flood lighting. Some targets appeared to be slowly moving and were found to be coming from tankers and container ships travelling along the far coast line. Hearing so many of these modulated lightwave signals was certainly an interesting experience and something I had not really expected. Even individual stars would produce a detectable 'hum' as the receiver/lens combination was aimed directly at them.
My one and only daylight test revealed extremely high levels of hum from the bright sky and, no doubt, front end overload desensitising....but the sudden sound of a buzzing bee in the headphones turned out to be just that, as the reflected light from its wings was being modulated by the rapid flap-rate....all very eye-opening to me and totally unexpected.
Here are some recent audio recordings made during a period of heavy cloud cover over Georgia Strait. All are on the far mainland coast or further inland and most sources were not visible to my eye.
- Landing aircraft strobes at Vancouver International ~ 30 miles.
- Aircraft over Georgia Strait, ~ 40 miles.
- Unidentified with odd repetition rate.
- Washington coast unidentified ~ 30+ miles.
- Washington coast unidentified 2.
- Washington coast unidentified 3.
I think such a system would make a wonderful 'science-fair' project for a budding student, complete with recordings....but perhaps it has all been done before!
For a very in-depth study of various current RX designs, see the Optical Receivers page of KA7OEI.
With all three receivers working well, the transmitters would be next....
On Making Nanowaves – Part 2
Now it seemed that up until just a few years ago, most amateur lightwave work had been done using lasers. The UK boys, as well as others, were now using LEDs, whose technology had made huge strides in recent years. The 'non- coherence' of LED light, unlike lasers, offered a distinct advantage when used for communications. Fading and signal dropout during periods of poor visibility were significantly reduced with the non-coherent LEDs when compared with laser light's 'all or nothing' characteristics.
Courtesy: KA7OEI As well, the thought of using lasers was somewhat scary in view of the growing amount of negative publicity from frequent reports of irresponsible use....combined with the fact that my path to VE7CA had to cross Vancouver International Airport!
Shining just a low-powered laser across this region was not something that I felt even remotely comfortable about doing. I felt much better about the project the more I learnt about LED's and of the good results being had by other experimenters.
Another exceptionally good source of valuable information (and probably the best on the Internet) is the 'optical' page site of Clint Turner, KA7OEI. Clint is an exceptionally gifted engineer-experimenter and is extremely generous in sharing his knowledge with others. As our local project developed over the course of many weeks, we exchanged several e-mails. My numerous questions would always result in very long detailed answers...and precise explanations for the reasons behind the answer or suggestions.
Just name any radio-related activity and Clint seems to be not only involved in it but has excelled in it. His willingness to share with others is just another example of why our hobby is so enjoyable!
While still deciding on receiver / transmitter designs, I built a small audio tone generator that would be needed, no matter what type of transmitter was eventually built. The plan was to have some method of making our signals stand out when searching for them in the noise. A distinctive two-tone FSK alert tone was decided upon as it could easily be built using a pair of 555's or a single 556. The final module allowed for three separate modes...an FSK 'beacon' mode, a keyed 'CW' mode and a short 'dash' mode (less annoying than the 'alert' tones).
Here is a recording of the FSK 'beacon' mode in action.
The base tone was set at about 600Hz since we preferred the lower tone for CW work.
No doubt there are other methods of building the FSK alert module but the 556 is simple and worked well.
For very weak-signal CW work, likely involving slow-speed (QRSS) modes in future 'non-line-of-sight' (NLOS) 'cloudbounce' trials, something with a bit more accuracy such as a crystal oscillator divided-down to audio frequencies would be better. Such a system would be very stable and provide a more precise modulation frequency... necessary for the narrow bandwidth viewing windows required for Argo or similar DSP audio viewers.
With the tone generator taken care of, the receiver was next on the list.
Shining just a low-powered laser across this region was not something that I felt even remotely comfortable about doing. I felt much better about the project the more I learnt about LED's and of the good results being had by other experimenters.
Another exceptionally good source of valuable information (and probably the best on the Internet) is the 'optical' page site of Clint Turner, KA7OEI. Clint is an exceptionally gifted engineer-experimenter and is extremely generous in sharing his knowledge with others. As our local project developed over the course of many weeks, we exchanged several e-mails. My numerous questions would always result in very long detailed answers...and precise explanations for the reasons behind the answer or suggestions.
![]() |
Clint Turner, KA7OEI |
Just name any radio-related activity and Clint seems to be not only involved in it but has excelled in it. His willingness to share with others is just another example of why our hobby is so enjoyable!
While still deciding on receiver / transmitter designs, I built a small audio tone generator that would be needed, no matter what type of transmitter was eventually built. The plan was to have some method of making our signals stand out when searching for them in the noise. A distinctive two-tone FSK alert tone was decided upon as it could easily be built using a pair of 555's or a single 556. The final module allowed for three separate modes...an FSK 'beacon' mode, a keyed 'CW' mode and a short 'dash' mode (less annoying than the 'alert' tones).
![]() |
Modulator mounted on TX |
![]() |
Courtesy: http://electronic-projects.50webs.com/p1.htm |
No doubt there are other methods of building the FSK alert module but the 556 is simple and worked well.
For very weak-signal CW work, likely involving slow-speed (QRSS) modes in future 'non-line-of-sight' (NLOS) 'cloudbounce' trials, something with a bit more accuracy such as a crystal oscillator divided-down to audio frequencies would be better. Such a system would be very stable and provide a more precise modulation frequency... necessary for the narrow bandwidth viewing windows required for Argo or similar DSP audio viewers.
With the tone generator taken care of, the receiver was next on the list.
On Making Nanowaves – Part I
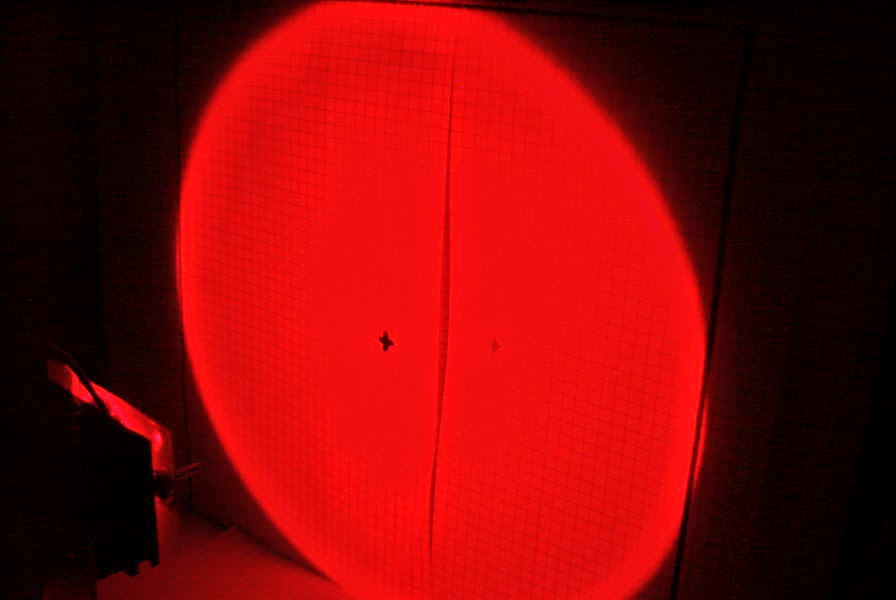
Over the course of many months, I had become intrigued by the lightwave experimentation being done by amateurs in the UK and particularly those being done by Roger, G3XBM. Like many of the UK builders, Roger had been building and testing simple low-power LED lightwave transmitters along with simple receiving systems. It was fascinating to follow his progress thanks to his daily blog (read his '481tHz' optical postings here) which documented every detail...both failures and successes. Even though not amateur radio per-se, to me it represented the best of what is so wonderful about our hobby and experimental homebrewing in particular. Unknowingly, Roger had me hooked and eventually I started to seriously contemplate building a lightwave system.
What finally pushed me over the building-brink was an amazing series of articles by Stuart Wisher (G8CYW) published in Radcom magazine and now available for download on Yahoo's "UK Nanowave Group". This four-part series was full of ideas, schematics and inspiration. I would challenge any homebrewer to read them without wanting to start building almost immediately! The group itself is an excellent source of circuits and up-to-date information regarding the latest activity amongst the UK amateur 'nanowavers'.
Now.... just having a lightwave system would not be much fun without having someone else to talk to. My first challenge was to find someone, preferably another ham, with whom I might be able to communicate once I had a system built and....they would need to be a homebrewer as well since none of this stuff was available 'off the shelf '. I contacted Markus (VE7CA), a very skilled homebrewer and sent him the series of Radcom lightwave articles. I did the same with John (VE7BDQ), another ardent builder and the main motivator (although he never knew it at the time) in me becoming hooked on ham radio as an early teenager. Both immediately called 'all-in'....our nanowave project was off and running!
Your LF Station’s Best Friend – The Scopematch PT.II

After building and installing the new Scopematch, a quick check of what I thought had been a properly-tuned system, surprisingly revealed that my 2200m antenna was neither matched correctly nor tuned to resonance! In spite of my poor-tuning (using the system shown in my last post), I had still received a number of encouraging reception reports from VE6, Washington and Oregon, giving me false and undeserved confidence in my earlier tuning attempts. The Scopematch soon changed all that.
The complete building instructions and operating description for the Scopematch may be found in "Tuning Aids for the 136kHz and 500kHz Bands" by Jim Moritz, MØBMU.
![]() |
Source: Tuning Aids for the 136kHz and 500kHz Bands by Jim Moritz, MØMBU |
As can be seen, a small RF sample taken by the Scopematch is coupled to the inputs of a dual-trace oscilloscope...one channel displaying the antenna current waveform and the other displaying the voltage waveform. When the antenna system has been tuned to resonance and matched to 50 ohms, both sine waves will be equal, in both phase and magnitude as shown below.
Such a condition is ideal and virtually guarantees that your transmitter is looking into a non-reactive 50 ohm load. Many transmitter designs utilized on LF employ inexpensive switching MOSFETs operating in either class-D or class-E modes that cannot tolerate any reactance in their output load. The end result of such a condition quickly produces a growing pile of dead MOSFETs!
![]() | |||
Source: Tuning Aids for the 136kHz and 500kHz Bands by Jim Moritz, MØMBU |
If the system is not tuned to resonance, the phase of the waveforms will not be the same and one waveform will lead the other. Whichever waveform is doing the leading indicates whether the antenna is tuned above or below the desired frequency so that proper corrective measures can be taken to achieve resonance.
Source: Tuning Aids for the 136kHz and 500kHz Bands by Jim Moritz, MØMBU |
The condition shown above illustrates the smaller waveform (V) lagging the larger current waveform (I) which indicates the antenna is capacitive or too high in frequency.With 'I' being greater than 'V', the resistive component of the load measures about 20 ohms.
The condition shown below indicates resonance but with 'V' being greater than 'I', the resistive component of the load measures about 80 ohms.
![]() |
Source: Tuning Aids for the 136kHz and 500kHz Bands by Jim Moritz, MØMBU |
The impedance match will be indicated by the amplitude of the two waveforms. Depending on which waveform is higher or lower indicates if the resistive impedance component is higher or lower than 50 ohms. Actual impedance values can be calculated from Ohm's Law using the sampled
waveform values.
It is fascinating to watch the scope patterns during windy conditions when the antenna's large tophat section is being blown around, causing slight changes in impedance and resonance. The two waveforms will expand and contract as well as shift phase slightly...almost as if the system is alive and breathing!
![]() |
My 2200m antenna - resonant and matched & a thing of beauty! |
Jim's article goes into much more depth as well as showing alternative methods of construction and is very much worth studying. Over the last few years I have suggested the Scopematch to several LFers who, like me, now wonder how they ever lived without it!
Your LF Station’s Best Friend – The Scopematch PT. I
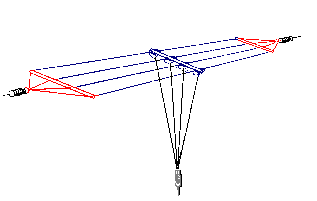
Several years ago, when I first set up my 2200m (136KHz) station under Industry Canada's Amateur Experimental Licensing Program, I utilized a fairly simple method shown in the LF Handbook, of attempting to tune and load my antenna. I had built a small top-loaded wire vertical consisting of a two-wire 50' flattop at the top end of a 30' vertical wire. A large loading coil of about 3 mH at the base of the antenna took care of getting the system close to resonance. As shown below, a variometer was used to fine-tune the system to resonance while the antenna impedance was matched to 50 ohms by tapping up from the base of the loading coil.
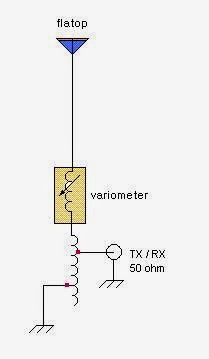
A 2A RF ammeter was used to monitor antenna current, with the plan being to tune and tap for maximum antenna current. It was the first time I had done any LF antenna work like this so it was a true 'learn as you go' project. It sounded fairly simple in theory but actual implementation was more challenging than I thought. What I also should have had was an LF SWR meter in the 50 ohm line as tuning and tapping for maximum antenna current did not guarantee that my system was indeed resonant or impedance matched. As you can imagine, there was much interaction between the two adjustments and I often found myself chasing my tail.
There were some tuning combinations that would peg the RF ammeter, indicating more current than my system was even capable of producing into a 50 ohm load. No doubt my settings were sufficiently 'off track' to create some diabolical impedance / off-resonance combination. I eventually settled on something that looked close but I was never really sure. Several weeks later I built the 'Scopematch' (designed by Jim Moritz -'MØBMU) and have not had a problem tuning and matching ever since.
Of all the devices in my LF toolbox, the most valuable by far is my Scopematch. Basically, it is a coupling device that allows you to monitor the tuning parameters of your LF antenna system. In real time, you are able to see both the impedance condition and the resonance tuning condition by observing the antenna current and voltage waveforms on a dual-trace oscilloscope. It is immediately apparent if your system is impedance matched (or not) and how close to resonance the system is. It will even tell you if your antenna is capacitive and requires more inductance to lower the frequency or if it is inductive and requires less loading inductance to bring it up in frequency.
Besides the dual-trace scope, the Scopematch requires only three parts and is fairly non-frequency critical. I am able to use it on both 2200m and 600m without any changes. More details to follow.
![]() |
My homebrew Scopematch |